Chemical
deburring, often referred to as electrochemical deburring (ECD), is an
advanced technique used to remove burrs and sharp edges from metal parts
through an electrochemical reaction. This method is particularly effective for
complex, intricate, or hard-to-reach areas (like inner holes or intersections),
where traditional mechanical deburring might be difficult or impractical.
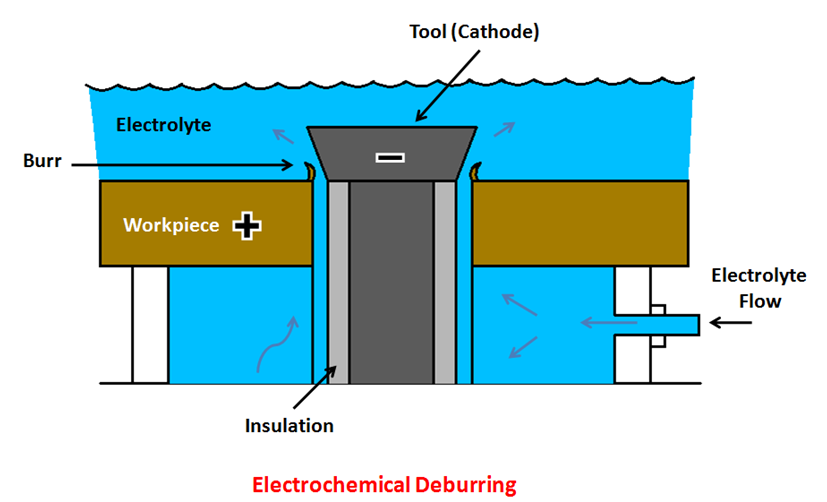
Working
Principle of Electrochemical Deburring (ECD)
The basic
principle of electrochemical deburring is the controlled removal of material
from a workpiece by an electrochemical reaction, where the burrs or sharp edges
are selectively removed through anodic dissolution (i.e., the process where
metal is oxidized and dissolved into a solution). The key components involved
are:
-
Anode (Workpiece): The
metal part (typically the workpiece containing burrs or sharp edges)
serves as the anode in the electrochemical process. The burrs or excess
material are located at specific areas of the workpiece, like sharp edges,
holes, or intersections.
-
Cathode (Electrode): A
specially designed cathode (usually a conductive tool or electrode) is
placed near the workpiece. The cathode is often shaped to match the
geometry of the part, especially around difficult-to-reach areas like
internal or crossing holes. The cathode is connected to the negative
terminal of the power supply.
-
Electrolyte Solution: The
electrochemical deburring process occurs in an electrolyte bath, which is
typically an aqueous solution of acids or salts (e.g., sodium nitrate or
sulfuric acid). The electrolyte acts as a medium to facilitate the
movement of ions and the electrochemical reactions.
-
Power Supply: A
direct current (DC) power supply is used to create a potential difference
between the anode (the workpiece) and the cathode (electrode). The voltage
applied is usually low (typically 10 to 30 volts, depending on the
material and size of the part).
Process
Overview:
-
Electrochemical Reaction:
-
When a DC voltage is applied
between the workpiece (anode) and the cathode, an electric current flows
through the electrolyte solution.
-
The part's burrs or sharp
edges, being at the highest points on the surface, become anodic
(positively charged).
-
The metal in these areas
undergoes oxidation, turning into metal ions and dissolving into the
electrolyte solution. This occurs preferentially on the burrs or sharp
edges because they have a higher surface energy and thus experience a
greater electrical potential.
-
Material Removal:
-
As the burrs dissolve, the
material is gradually removed from the workpiece, leaving the remaining
surfaces smooth and free of sharp edges.
-
The removal rate is
selective, meaning the process predominantly affects the high points
(burrs) and not the rest of the workpiece, allowing the core material to
remain intact.
-
The material is removed in a
controlled manner, and the process can be tailored to remove only the
burrs without significantly affecting the part's overall geometry.
-
Deburred Surface:
-
After a sufficient amount of
time has passed, the burrs are eliminated, and the remaining surface
becomes smooth.
-
The process can be stopped at
any time, depending on the desired surface finish and the extent of burr
removal.
Key
Features of Electrochemical Deburring:
-
Precision: ECD
can precisely remove burrs without affecting the overall geometry or
dimensions of the part. It’s especially useful for intricate or
hard-to-reach areas (like inner holes or corners).
-
Selective Material Removal: The
process is highly selective, meaning it targets only the burrs and sharp
edges, leaving the rest of the workpiece unaffected.
-
No Mechanical Force:
Since the deburring is done through a chemical reaction and not mechanical
abrasion, there is minimal risk of damaging delicate features or
introducing additional stresses into the material.
-
Minimal Heat Affected Zone:
Unlike other thermal processes (such as laser or flame deburring),
electrochemical deburring generates very little heat, reducing the risk of
thermal distortion or damage.
-
No Tool Wear:
Because there is no physical contact between the workpiece and the tool,
the process does not cause tool wear, which is common in mechanical
deburring methods.
Steps
Involved in the Electrochemical Deburring Process:
-
Preparation: The
workpiece is placed into a fixture or holder, ensuring that it remains in
a fixed position during the deburring process. The part is connected to
the anode (positive terminal) of a DC power supply.
-
Electrode Setup: The
cathode (electrode) is shaped to match the geometry of the workpiece,
especially the internal holes or areas to be deburred. The electrode is
connected to the negative terminal of the DC power supply.
-
Electrolyte Bath: The
workpiece is submerged in an electrolyte bath, which serves as the medium
for the electrochemical reaction. The electrolyte is carefully chosen
based on the material of the workpiece and the desired deburring effect.
-
Applying Current: Once
the workpiece and electrode are in place and the electrolyte is flowing, a
controlled DC current is applied. The electrochemical process begins, and
the burrs are selectively dissolved away.
-
Monitoring and Control: The
process is typically monitored using sensors or visual inspections to
ensure that the burr removal is occurring at the right rate. The time and
current are carefully controlled to avoid over-deburring or damaging the
part.
-
Post-Deburring Cleaning:
After the deburring process, the workpiece is removed from the electrolyte
bath, cleaned to remove any residual electrolyte, and inspected for burr
removal quality.
Advantages
of Electrochemical Deburring:
-
Effective for Complex
Geometries: ECD is particularly suited for deburring
intricate shapes, internal cavities, and intersecting holes that are
difficult to reach using traditional methods.
-
No Physical Contact:
There is no mechanical wear or contact, reducing the risk of surface
damage, distortion, or work-hardened surfaces.
-
High Precision: The
process can achieve high precision in deburring without altering the rest
of the workpiece's geometry.
-
Fast Process: It
can quickly deburr parts, especially when compared to manual methods or
traditional mechanical processes.
Disadvantages:
-
Setup Cost and Complexity: The
equipment for electrochemical deburring can be expensive and requires
skilled operators. The electrolyte bath must also be carefully maintained.
-
Material Limitations: The
process is more effective on conductive metals (like stainless steel,
titanium, aluminum, copper, etc.) and may not be suitable for non-metallic
materials or non-conductive metals.
-
Environmental Concerns: The
electrolyte solutions used in ECD can be hazardous and require proper
disposal or recycling to avoid environmental contamination.
In summary, electrochemical deburring is a precise, efficient method for removing
burrs from metal parts, especially in complex geometries or hard-to-reach
areas. It uses an electrochemical reaction to selectively remove material from
burrs, leaving the rest of the part's surface intact.
For more information about ECM machines, please feel free to contact us.
Bob Li
Mobile(Whats app): +86-13338697597
Tech EDM Trade Co., Ltd
Tel: +86-512-68782578
Fax:+86-512-66671799
Email: sale@techedm.com
Email: edmachining@hotmail.com
Add: No. 58 Huajin Rd, 215153, Suzhou, China
www.techedm.com