Wire EDM
(Electrical Discharge Machining) machines are widely used in manufacturing for
their precision and versatility. However, like any technology, they have both
advantages and disadvantages. Here’s a detailed overview:
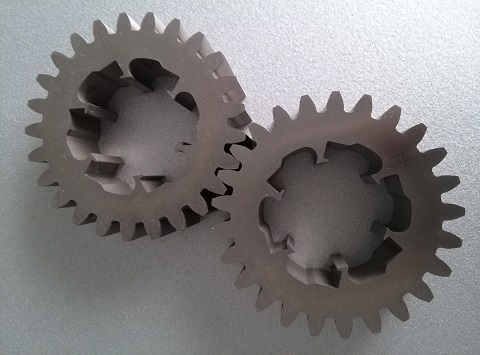
Advantages
of Wire EDM Machines
-
High Precision and Accuracy:
-
Wire EDM machines can achieve
extremely tight tolerances, often within ±0.005 mm, making them ideal for
intricate designs and complex geometries.
-
Complex Geometries:
-
Capable of cutting complex
shapes, including sharp internal corners and small radii that are
difficult or impossible to achieve with conventional machining methods.
-
Minimal Workpiece Distortion:
-
The process generates minimal
heat-affected zones, reducing the risk of warping or altering the
physical properties of the workpiece material.
-
Variety of Materials:
-
Wire EDM can work with a wide
range of conductive materials, including hardened steels, titanium, and
exotic alloys, which may be challenging for other machining processes.
-
No Tool Wear:
-
Unlike traditional cutting
tools, wire EDM does not experience mechanical wear, leading to
consistent cutting performance and reduced downtime for tool changes.
-
Clean Process:
-
The process is relatively
clean, as it does not produce chips or debris like traditional machining.
The use of dielectric fluid also helps keep the workspace clean.
-
Automation Capabilities:
-
Many modern wire EDM machines
offer CNC automation, allowing for unattended operation and increased
production efficiency.
-
Versatile Applications:
-
Suitable for a variety of
applications, including mold making, aerospace components, automotive
parts, and intricate medical devices.
-
Good Surface Finish:
-
Produces a smooth surface
finish, which often requires little to no post-processing.
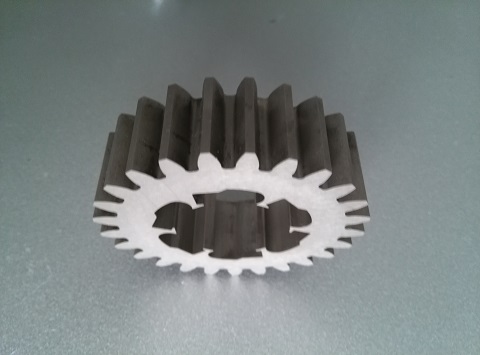
Disadvantages
of Wire EDM Machines
-
Speed Limitations:
-
Wire EDM is generally slower
than conventional machining methods, especially for thicker materials or
large workpieces.
-
Cost:
-
The initial investment for
wire EDM machines can be high, and operating costs, including maintenance
and dielectric fluid, can also add up.
-
Material Thickness Limitations:
-
While wire EDM excels at thin
materials, it can be less effective for very thick materials, as cutting
speeds decrease significantly.
-
Limited to Conductive
Materials:
-
Wire EDM can only process
conductive materials, excluding non-conductive materials like plastics,
ceramics, and wood.
-
Dielectric Fluid Dependency:
-
The process requires
dielectric fluid for effective operation, which can lead to additional
costs and environmental considerations regarding fluid disposal.
-
Complex Setup:
-
Setting up a wire EDM machine
can be more complex compared to conventional machining, requiring skilled
operators to program and calibrate the machine.
-
Wire Breakage:
-
Wire breakage can occur,
particularly when cutting very intricate parts, leading to production
delays and the need for adjustments.
-
Surface Residue:
-
The use of dielectric fluid
can sometimes leave a residue on the workpiece, requiring cleaning after
machining.
Summary
Wire EDM
machines are powerful tools for precision machining, offering unique advantages
for complex and high-precision applications. However, they also come with
limitations, particularly in terms of speed and cost. The decision to use wire
EDM should consider these factors in relation to the specific requirements of
the project and the characteristics of the materials involved.
For more information about the wire cut EDM machines, please feel free to contact us directly.
Bob Li
Mobile(Whats app): +86-13338697597
Tech EDM Trade Co., Ltd
Tel: +86-512-68782578
Fax:+86-512-66671799
Email: sale@techedm.com
Email: edmachining@hotmail.com
Add: No. 58 Huajin Rd, 215153, Suzhou, China
www.techedm.com